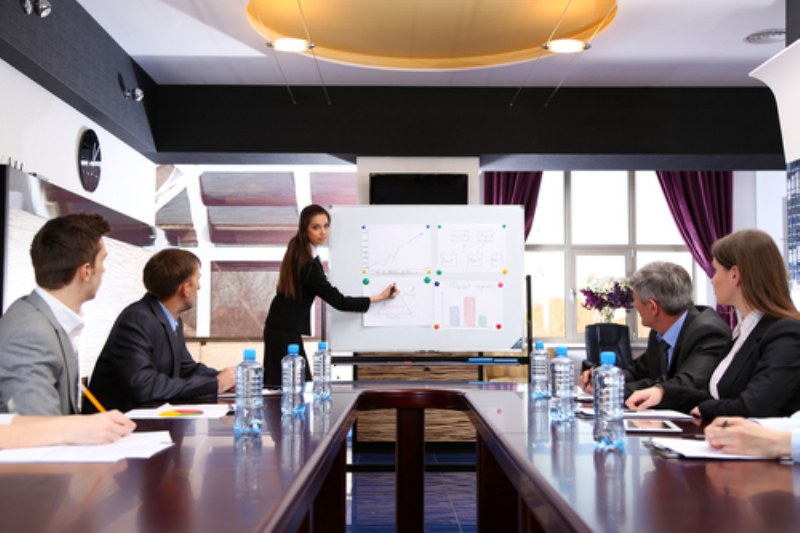
Affinchè un’impresa possa crescere e ottenere risultati sempre migliori nel corso del tempo, di cruciale importanza che la proprietà, il management e il personale sappiano gestire al meglio tutta una serie di aspetti, quali l’analisi dei problemi, l’efficienza del sistema produttivo, la raccolta delle idee, la pianificazione e la rappresentazione dei flussi di lavoro. Quando un’azienda è organizzata al meglio, riesce a sfruttare il tempo a disposizione e a centrare gli obiettivi prefissati. Il segreto per avere successo in tutto ciò sta nel trovare una sorta di routine, data da un metodo, perfettamente in linea con il proprio business.
Pertanto, affinché l’impresa possa ottenere vantaggio competitivo, gran parte dei risultati non passa solamente dai prodotti messi in commercio o dai servizi erogati, ma dalla valorizzazione del personale. Dipendenti soddisfatti e motivati danno sempre il massimo sul posto di lavoro. Quindi, con un management e una proprietà che hanno ottima leadership, con una comunicazione interna chiara, con criteri di valutazione meritocratici e con la cultura dei feedback, dove si cerca il parere di chi ha uno specifico know-how, ci sono maggiori possibilità di lavorare bene.
Qual è pertanto il miglior metodo di miglioramento per organizzare l’azienda? Dare una risposta secca al seguente interrogativo è cosa piuttosto complessa, per il semplice motivo che vi sono troppi fattori in ballo che variano da caso a caso: il settore di riferimento, il core business, la grandezza, la struttura, il contesto geografico, il target di riferimento sono solo alcuni di questi.
Presentiamo, pertanto, alcuni metodi di successo con cui l’organizzazione aziendale può andare incontro a un’importante svolta.
Il metodo Kaizen
Un metodo di organizzazione aziendale che, dopo aver riscosso un importante successo in Giappone, è stato importato nelle principali multinazionali statunitensi e poi via via anche in alcune piccole realtà imprenditoriali, garantendo risultati di livello organizzativo decisamente degni di nota. Per la precisione, fu la Toyota all’inizio degli Anni ’80 a introdurre questo metodo, coniato dal manager Masaaki Imai.
KAI sta per cambiamento e miglioramento, mentre ZEN stta per buono, migliore. Quindi, traducendo alla lettera Kaizen si ha miglioramento continuo.
Il Kaizen, pertanto, viene interpretato come una serie di tecniche, il cui scopo primario consiste nel facilitare il pensiero, l’analisi e il miglioramento continuo tramite il ruolo dei lavoratori. Occorre saper cambiare di giorno in giorno alla ricerca della perfezione. Quest’ultima non deve avere mai fine.
Ciò che contraddistingue il Kaizen è che non necessita di investimenti evidenti per poter essere implementato a livello aziendale. Tuttavia, affinché vengano eliminate le inefficienze e gli sprechi, è bene ottimizzare le risorse a disposizione.
Qual è il principio cardine del Kaizen? Far bene al primo colpo attraverso un’attività a prova di errore. Gli sbagli, i difetti, le incomprensioni non sono altro che un’attività non eseguita in maniera corretta che determina instabilità e inaffidabilità in termini di processo. Pertanto, l’errore che ne deriva è dovuto sempre a una mancata rilevazione e a una non correzione.
Come specificato, l’eliminazione del problema avviene attraverso la capacità di perseguire la perfezione continua. Mettersi a indagare sulle cause alla ricerca di ciò che non va e a porre in essere lazione correttiva che ripristinerà la situazione alla normalità è ciò che comunemente avviene con il Kaizen. Il miglioramento, quindi, si ottiene solo sul campo, controllando durante il processo lavorativo quali sprechi ci sono e verificando i miglioramenti che possono diventare con il passare del tempo parte integrante della cultura aziendale.
Punti cardine del Kaizen sono la messa in discussione del metodo lavorativo attuale, la ricerca continuativa del miglioramento processuale, la capacità di saper coltivare l’iniziativa dei dipendenti, l’approccio di tipo proattivo, la definizione dei correttivi, i follow-up dei cambiamenti attuati, la messa a punto di procedure chiare, la definizione di obiettivi concreti e realistici e infine il gioco di squadra.
Il Kaizen infine è un metodo lavorativo che migliora complessivamente il know-how aziendale, perché aiuta i dipendenti e il management a uscire da una sorta di comfort zone e a pensare in maniera divergente. Solo così si hanno tutti i presuppsti per poter semplificare i flussi lavorativi.
Il cambiamento in azienda deve avvenire senza alcun tipo di rischio e in assenza di vincoli: solo in questo modo, il miglioramento può essere continuo. Più si è efficaci, tanto più si è spinti a dare il massimo. Questa è la sfida del Kaizen e dei suoi miglioramenti progressivi.
La filosofia 5S
Una metodologia di organizzazione del lavoro aziendale che prende il meglio dalla cultura giapponese, dalla programmazione gestionale e dall’attenzione alla qualità teorizzata negli Stati Uniti d’America e dalla filosofia francese dei primi dell’Ottocento. L’intento di fondo del metodo 5S, pertanto, ruota attorno all’identificazione di una procedura di natura sistematica e facilmente ripetibile nell’ottica della gestione degli ordini. Ciò che ne deriva è, da un lato, il miglioramento delle prestazioni operative e, dall’altro, il raggiungimento della standardizzazione dell’ottimizzazione.
Ma cosa indicano queste 5 S? Per spiegarlo in modo accurato, vengono riportati i termini in giapponese, in inglese e in italiano.
SEIRI / Sort / Semplificazione, scelta e separazione: il primo passaggio è quello di lavorare in un ambiente produttivo. Affinché ciò sia cosa fattibile, è bene catalogare la strumentazione di lavoro, puntando solo su ciò che serve effettivamente e rinunciando a tutto ciò di cui non si ha bisogno.
SEITON / Set in order / Sistema di ordine e di organizzazione: per un’identificazione immediata e per un accesso facile, è bene posizionare l’attrezzatura lavorativa al posto giusto. In questo modo, non si spreca tempo e si è più produttivi.
SEISO / Shine / Splendere: la propria postazione lavorativa deve splendere. Va tenuta pulita e in ordine.
SEIKETSU / Standardize / Standardizzaazione: se si creano procedure standardizzate e di routine per tenere ordinato il contesto lavorativo, i risultati non tarderanno avvenire. La forza lavoro apparirà più produttiva, a patto che i principi fin qui presentati vengano applicati con cura.
SHITSUKE / Sustain / Sostenimento continuo; fare in modo che questa metodologia diventi abitudinaria nel lavoro giornaliero e che vengano fatti rigorosi controlli è la soluzione giusta per il prosieguo.
L’origine di questo metodo organizzativo, come si può facilmente intuire, era correlato alla pulizia della postazione di lavoro nell’ottica di rendere migliori le prestazioni lavorative. Applicando il metodo 5S su larga scala va precisato che ogni giorno qualsiasi impresa si trova dinanzi a decisioni da prendere e a controlli volti a garantire il mantenimento dell’efficienza del flusso lavorativo. Tutto deve essere al posto giusto e ciò che non è conforme va prontamente segnalato in modo visivo. D’altronde, con procedure chiare, semplici e condivise da tutti, riordinare gli spazi e ridurre i tempi di attesa diventa la sfida da vincere per le imprese: in molti casi, si sono evitati sprechi relativi alla movimentazione dei beni e, di conseguenza ottimizzazione del personale e risparmio considerevole di risorse. Inoltre, le imprese che hanno applicato il 5S hanno ridotto i rischi di infortuni, migliorato sensibilmente la sicurezza sul posto di lavoro, resto il contesto maggiormente ergonomico, rimosso i difetti in fase di produzione, rinunciato ad attrezzature non idonee e ottimizzato le tempistiche. Meglio di così?
La Lean Production
Per essere considerata efficiente, la produzione aziendale deve essere organizzata al meglio. Solo così il processo lavorativo può essere condotto in modo preciso, dicendo addio definitivamente agli sprechi di risorse e di tempo. L’organizzazione aziendale deve essere snella e minimizzare gli sprechi, fino a quando non li si elimina alla radice.
Punto di partenza del metodo della Lean Production è che a delineare il concetto di valore è il cliente e non i produttori. Una volta identificate tutte quelle attività in grado di garantire valore aggiunto per il cliente, si lavora sull’individuazione degli sprechi. Molti di questi hanno strettamente a che fare con la sovrapposizione. Grazie a una produzione regolarizzata, incentrata sul miglioramento del valore dei prodotti messi sul mercato o dei servizi erogati, il consumatore finale apprezzerà i risultati ottenuti.
L’esempio più classico dei traguardi raggiunti dalla Lean Production si riferiscono all’eliminazione dei danni, causati dalle scorte a magazzino che restano invendute. Trattasi di una perdita importante, in quanto un certo capitale risulta immobilizzato. Solo se il ciclo produttivo va incontro a una ripresa, si registra un aumento delle vendite e, di fatto, lo smaltimento delle scorte.
Il processo produttivo deve essere flessibile, dimostrandosi spinto o tirato nei confronti del cliente, a seconda delle fasi storiche, Non è un’iperbole asserire che, secondo la Lean Production, un’impresa funziona come un’auto che per poter esprimere prestazioni di alto livello deve essere correttamente alimentata, gestita in maniera ottimale e beneficiare dei lavori di revisione di manutenzione periodici.
Non si guarda né alla standardizzazione e né tanto meno la distribuzione push. Tutto parte da un analisi di prodotto che va realizzato da personale qualificato. Solo in questo modo, il cliente apprezzerà il valore aggiunto, derivante dall’utilizzo di quanto acquistato. In questo modo, il perseguimento di interessanti obiettivi in termini di crescita non sarà un’utopia per le aziende che applicano la Lean Production, ma un dato di fatto.
Kaikaku
Per quanto i piccoli miglioramenti possano apportare risultati degni di nota, non è detto che alla fine garantiscano il cambiamento tanto atteso. Questo è in sintesi l’assunto di fondo del metodo Kaikaku, considerato sotto certi aspetti agli antipodi del Kaizen. Kaikaku, non a caso, sta per riforma o meglio ancora per cambiamento radicale. L’insieme di tutta una serie di azioni pianificate a monte e coordinate nei minimi dettagli può dare luogo a un nuovo corso. Tuttavia, un cambiamento radicale, introdotto dal Kaikaku, non è qualcosa di ordinario che viene fatto tutti i giorni. Al contrario è un’azione straordinaria che mira ad assicurare un impatto maggiore, specie per ciò che concerne la lotta agli sprechi.
La ristrutturazione dei sistemi di produzione è il classico esempio di innovazione introdotta dal Kaikaku. Altre volte, nel momento in cui la situazione finanziaria di un’impresa appare alquanto critica, il metodo del Kaikaku può apparire la soluzione necessaria per allocare meglio le risorse e ridefinire le mansioni del personale. Pur essendo agli antipodi del Kaizen, il Kaikaku non ne esclude il ricorso. Spesso, nella cultura giapponese, il Kaizen viene paragonato a una pioggia estiva, mentre il Kaikaku a un acquazzone. Essendo un metodo “calato dall’alto” e di approccio top-down, il Kaikaku presuppone meno interrogativi in attesa di vedere gli impatti effettivi di quanto pianificato.
Reingegnerizzazione dei processi aziendali
Altro metodo organizzativo, contraddistinto da una trasformazione radicale, affinché produttività, efficienza e alto livello qualitativo dei prodotti realizzati e dei servizi forniti da un’impresa appaiano all’ordine del giorno.
La reingegnerizzazione dei processi aziendali si differenzia dalla riprogettazione dei processi, perché non si basa sul miglioramento contino, ma su un riassetto drastico in termini di dinamiche di lavoro. A volte a essere concettualizzata di nuovo è l’intera organizzazione lavorativa.
In questo metodo di organizzazione lavorativa, i cambiamenti hanno una vasta portata e si verificano in maniera rapida. L’impatto sulla qualità dei prodotti e dei servizi appare decisamente significativo, perché i processi precedenti vengono rimossi intenzionalmente, perché identificati come obsoleti.
A fronte di decisione giuste e di una corretta implementazione dei processi, la reingegnerizzazione apporta benefici tangibili di primo acchito: efficacia ed efficienza possono rappresentare la tanto attesa svolta. Tuttavia, non è detto che i suddetti cambiamenti drastici vengano accettati all’unisono da tutti. Le difficoltà di adattamento e i continui disagi, oltre all’inadeguatezza del personale, possono rappresentare un ostacolo insormontabile. Inoltre, occorrono investimenti davvero notevoli.
Questi, in definitiva, sono 5 dei tanti metodi (esiste anche il facility management ad esempio) di miglioramento continuo o di cambiamento radicale che esistono per organizzare al meglio l’azienda e aumentare produttività, raggiungere obiettivi. Alcuni puntano sul miglioramento continuo, altri su cambiamenti radicali. Non c’è una scelta giusta di un metodo a discapito di un altro, ma solo casi di successo e situazioni meno fortunate.