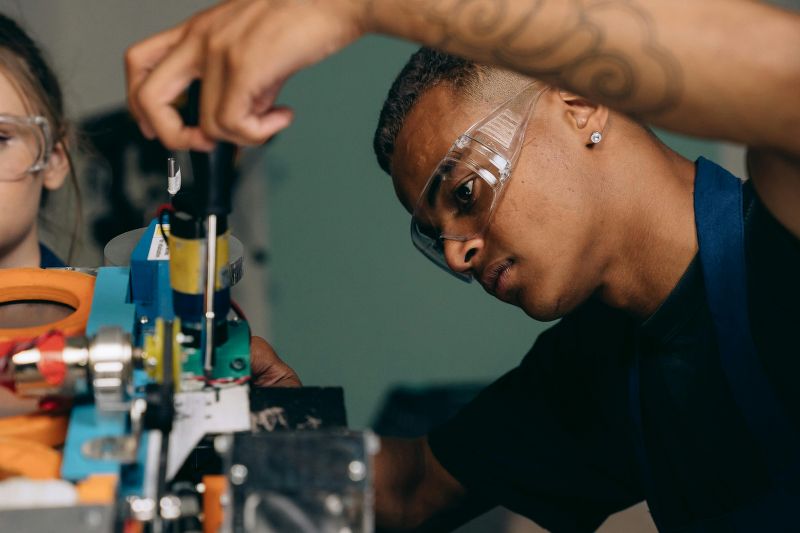
La manutenzione preventiva dei macchinari è un aspetto fondamentale per ogni azienda che punta a mantenere alta la produttività e a garantire la sicurezza dei propri dipendenti.
In molte realtà industriali, i macchinari sono soggetti a un utilizzo talmente intenso che, senza interventi periodici, possono andare incontro a malfunzionamenti, guasti o addirittura incidenti.
Implementare un piano di manutenzione preventiva efficace permette di ridurre al minimo i tempi di fermo, di aumentare la durata dei macchinari e di ottimizzare le risorse aziendali.
Cos’è la manutenzione preventiva e perché è importante?
La manutenzione preventiva consiste in una serie di interventi programmati sui macchinari, mirati a verificare e ripristinare il corretto funzionamento delle componenti prima che si verifichi un guasto. A differenza della manutenzione correttiva, che interviene solo quando il macchinario si è già rotto, quella preventiva si basa su controlli e sostituzioni programmate, riducendo così l’incidenza di malfunzionamenti improvvisi.
Questa pratica non solo migliora la produttività, evitando interruzioni improvvise, ma si traduce anche in un risparmio economico a lungo termine: la riparazione di un guasto grave, infatti, spesso comporta costi elevati, senza contare il danno derivante da un impianto fermo. Inoltre, aiuta a prolungare il ciclo di vita dei macchinari, migliorando così l’efficienza dell’investimento aziendale.
Come organizzare un piano di manutenzione preventiva
Per impostare un piano di manutenzione efficace, è essenziale che l’azienda segua alcune linee guida. Innanzitutto, è necessario conoscere le specifiche tecniche e le esigenze di ogni macchinario, che spesso richiedono interventi e controlli differenti. Ad esempio, un tornio (tra le macchine utensili più usate) e una pressa idraulica necessitano di manutenzioni diverse, a causa delle componenti specifiche e delle differenti sollecitazioni meccaniche cui sono sottoposti.
Una buona prassi è la creazione di un calendario che comprenda tutte le attività di verifica e pulizia ordinaria, oltre alle eventuali sostituzioni programmate delle parti più soggette a usura.
La qualità dei materiali di assemblaggio e dei componenti riveste un ruolo fondamentale per garantire la durabilità dei macchinari: componenti come gli inserti filettati, vengono usati per garantire sicurezza e durata nelle parti soggette a frequente usura. Questi piccoli componenti permettono di fissare saldamente le viti e gli elementi di collegamento, evitando che si allentino o che danneggino il macchinario stesso con l’uso continuato.
I benefici della manutenzione preventiva
Ecco una panoramica dei principali benefici:
- Riduzione dei tempi di fermo: quando i macchinari si guastano, l’azienda è costretta a fermare la produzione fino alla riparazione con conseguenti costi aggiuntivi e ritardi nelle consegne. Con una manutenzione preventiva ben pianificata, è possibile ridurre drasticamente i tempi di fermo, poiché i controlli periodici riducono la probabilità di guasti improvvisi.
- Aumento della sicurezza: la sicurezza dei dipendenti, come ben spiegato in questo articolo, è una priorità per ogni azienda. Una corretta manutenzione assicura che le apparecchiature siano sempre in condizioni ottimali, riducendo la possibilità di malfunzionamenti che potrebbero causare danni o lesioni.
- Miglioramento della qualità del prodotto: macchinari efficienti e ben mantenuti garantiscono una produzione continua e di qualità, mentre macchinari soggetti a malfunzionamenti potrebbero compromettere la qualità dei prodotti. La manutenzione preventiva è quindi anche un’alleata per il controllo qualità, aiutando a mantenere elevati gli standard produttivi.
Inoltre, riparare un guasto grave è spesso molto più costoso rispetto a piccoli interventi programmati. Una manutenzione periodica permette di identificare eventuali anomalie prima che diventino problemi complessi, riducendo così le spese di riparazione e prolungando la vita dei macchinari.