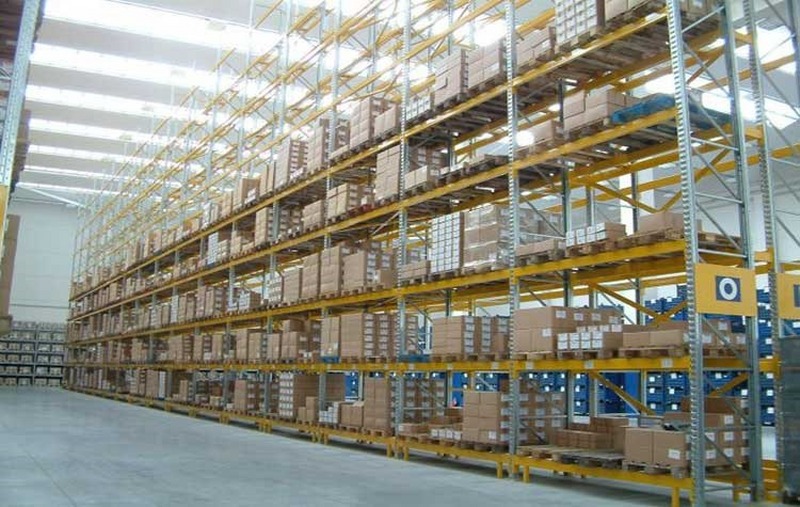
La sicurezza sul lavoro è un tema molto scottante quindi per un responsabile della logistica è di fondamentale importanza conoscere tutte le normative legate a questo settore per attuare le disposizioni necessarie a tutelare l’incolumità dei dipendenti e della merce. Segnaletica, scarpe antinfortunistiche, caschetti ed attrezzature adeguate rappresentano l’ABC che ogni operatore e dipendente dovrebbe conoscere, ma sono diversi gli aspetti da tenere in considerazione per ridurre i rischi e garantire lo svolgimento del lavoro in totale sicurezza. Per quanto riguarda la sicurezza in magazzino i punti da considerare sono fondamentalmente 5: formazione, prevenzione, responsabilità, manutenzione ed ispezione tecnica. Analizziamo step by step ogni singolo punto per garantire la massima sicurezza sul posto di lavoro.
La formazione del personale
Il personale, prima di tutto, ha il compito di badare alla propria incolumità e per questo motivo deve essere opportunamente formato con corsi continuativi e regolari e conoscere perfettamente i manuali di sicurezza di ogni impianto. Se un dipendente riscontra un’anomalia, un malfunzionamento o un deterioramento di un’attrezzatura specifica o di un impianto deve immediatamente avvisare il supervisore della sicurezza per tutelare l’incolumità personale, dei propri colleghi e della merce stipata in magazzino. In questo articolo è possibile approfondire il ruolo del datore di lavoro nei confronti della sicurezza.
Prevenzione e valutazione dei rischi
La prevenzione degli incidenti sul lavoro passa inevitabilmente per la valutazione dei rischi, in base alla quale bisogna adottare le giuste contromisure. Il primo step riguarda l’identificazione dei rischi che richiede un monitoraggio di tutte le attrezzature ed i locali del magazzino.
Dopo aver valutato i rischi bisogna assegnare delle priorità e stabilire quali sono i lavori più urgenti da fare per mettere in sicurezza l’intero ambiente lavorativo. A questo punto bisogna pianificare gli interventi da eseguire e adottare le misure necessarie, tenendo conto di alcuni fattori come l’usura dei macchinari, gli spazi necessari entro cui operare e alcune situazioni contingenti come perdite di liquido che possono creare condizioni potenzialmente pericolose. Per completare il processo di prevenzione e valutazione dei rischi è opportuno monitorare e revisionare le attrezzature e le apparecchiature per mantenerle sempre in ottimo stato tramite appositi lavori di manutenzione che devono essere svolti da un personale formato, competente e qualificato.
La responsabilità secondo la normativa europea
In base alla normativa europea le responsabilità relative al sistema di stoccaggio e le scaffalature vanno suddivise tra fornitore ed utilizzatore.
Il fornitore delle scaffalature in base alle direttive del cliente deve considerare gli elementi relativi alla distribuzione ed al calcolo delle merci per un utilizzo adeguato delle attrezzature. Ha inoltre il compito di fornire prodotti certificati e una consulenza adeguata relativa agli accessori aggiuntivi da utilizzare per la messa in sicurezza della scaffalatura. Infine deve valutare con esattezza i carichi che il pavimento è in grado di tollerare e dotare l’utilizzatore dei carrelli di portata che devono riportare esattamente le caratteristiche dell’impianto.
L’utilizzatore delle scaffalature deve innanzitutto valutare i rischi effettivi durante l’utilizzo per prevenire ogni danno o incidente a cose e persone. Ha inoltre il compito di fornire al personale la formazione adeguata per la movimentazione e l’utilizzo delle attrezzature e assicurarsi che tutte le operazioni vengano svolte secondo le indicazioni del fornitore. Deve quindi nominare un PRSES (Person Responsible for Storage Equipment Safety), vale a dire un supervisore della sicurezza dei lavoratori ed infine garantire una manutenzione continua delle scaffalature e delle attrezzature di stoccaggio.
Gli step fondamentali per la manutenzione
Altro passaggio fondamentale per la sicurezza del lavoro è la manutenzione che prevede 3 step: ispezioni periodiche per il rilevamento, comunicazione e registrazione di eventuali anomalie o malfunzionamenti. Il programma di manutenzione deve essere aggiornato se cambiano i carichi di lavoro.
Il personale di magazzino tramite un’ispezione quotidiana deve monitorare costantemente il luogo di lavoro e individuare malfunzionamenti o anomalie immediatamente visibili e tangibili per poi procedere immediatamente alla sostituzione o alla riparazione dell’attrezzatura malfunzionante.
Il responsabile della sicurezza deve effettuare un’ispezione settimanale per verificare lo stato della struttura e delle attrezzature di stoccaggio e segnalare gli eventuali danni.
É compito del responsabile di sicurezza anche eseguire un’ispezione mensile per valutare il livello generale di sicurezza all’interno del magazzino e comunicare eventuali danni o malfunzionamenti. Il PRSES deve interfacciarsi continuamente con il fornitore dei sistemi di stoccaggio per comprendere le caratteristiche degli impianti e valutare le prestazioni se dovessero cambiare i carichi.
I tre livelli di rischio assegnati agli elementi danneggiati
Gli elementi danneggiati possono essere valutati con tre livelli di rischio: rosso, arancione e verde.
In caso di etichetta rossa i danni riscontrati sono piuttosto gravi ed è richiesto un intervento immediato. In tal caso gli elementi danneggiati dovrebbero essere sostituiti piuttosto che riparati.
L’etichetta arancione evidenzia una situazione potenzialmente pericolosa e quindi richiede un intervento piuttosto tempestivo.
L’etichetta verde indica una situazione sotto controllo che rispecchia i requisiti di sicurezza, ma è opportuno valutare ed esaminare gli elementi nelle future ispezioni.
L’ispezione tecnica
Il proprietario del magazzino in base alla norma EN 15635 è obbligato a contattare tecnici qualificati per effettuare un’ispezione annuale sulle scaffalature metalliche e valutare lo stato di ogni singolo componente.
I tecnici qualificati devono innanzitutto verificare le condizioni generali delle scaffalature e del pallet per valutarne lo stato. Nel corso dell’ispezione vanno monitorati i carrelli elevatori e la visibilità dei cartelli di portata che devono essere conformi alle scaffalature utilizzate. I tecnici devono controllare l’esecuzione corretta delle operazioni e delle manovre da parte dei dipendenti, lo stato generale di pulizia e ordine nei corridoi ed eventuali crepe o cedimenti nei pavimenti. Dopo l’ispezione i tecnici devono rilasciare un report approfondito ed esaustivo indicando, laddove necessario, gli interventi da eseguire.
Per avere una panoramica completa sulle dotazioni necessarie alla messa in sicurezza in magazzino e per ricevere ulteriori informazioni sulla normativa si può visionare il sito Emme Cinque, azienda specializzata nella distribuzione e nella fornitura di attrezzature industriali e prodotti per la sicurezza. A questo, è sembre bene affiancare la consulenza di un professionista serio, in quanto il mancato rispetto di queste normative, può comportare multe salate o addirittura la chiusura dell’attività.